Key Facility Considerations for Meeting Biologics Demand
Add bookmark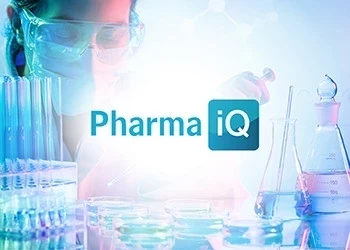
As biologic and biosimilar production becomes big business, re-equipping facilities originally built for traditional chemical production is essential for compliance and product consistency.
With the market for biologic and biosimilar medicines growing rapidly, traditional pharmaceutical manufacturing facilities and facilities management practices are fast becoming obsolete. Where small-molecule production facilities are relatively easy to transition from production of one drug to another, transitioning to biologic production is a complex undertaking. Yet, the major life science companies are finding they must fully transform their real estate portfolios from traditional small-molecule production environments to more sophisticated biologics laboratory settings that can accommodate the rigorous regulatory oversight required for storing and handling sensitive living tissues.
Building a new or outfitting an existing facility to support biologics systems is a mammoth undertaking by any measure. The following questions are key issues facing life sciences companies as they update their facilities strategies.
Pharma IQ: How does compliance differ for biologic versus chemical facilities?
R Humphrey: Biologics are directly affected by source material characteristics and handling. To assure consistent quality, facility and regulatory requirements are considerably more stringent than for traditional drug production. As the FDA notes in its FAQ document on biologics, "since there is a significant difference in how biological products are made, the production is monitored by the agency from the early stages to make sure the final product turns out as expected."
To be in compliance, facility designs must be reviewed before a biologics program can begin. It must also be ready for audits and safety inspections at any time. The same complex facility and regulatory requirements apply to biosimilars, too, as they may use an entirely different kind of living tissue and process than the prior product.
Pharma IQ: Which facility activities are most important for compliance considerations?
R Humphrey: A range of facilities management best practices lead to better compliance and product consistency. Some of the key considerations include:
- Air quality and filtration: Particulate counts must remain within acceptable parameters,making environmental monitoring essential. Air flow is also important: Biologics facilities require more than 20 air changes per hour with no recirculation, a much higher rate than is needed in chemical-based labs. Moreover, in facilities, developing more than one product, air flow systems must be separate for each area.
- Cleaning protocol. Sterilization of all surfaces is required more frequently in biologics facilities than in many chemical labs. And to prevent potentially dangerous organisms from developing a resistance to the cleaning solution, multiple disinfectants must be used in rotation.
- Environmental control:When handling cells, tissue and other organisms, it is vital to maintain a consistent temperature and environment. For example, gowned areas are required for “clean” entry and “dirty” exits from lab areas, and some types of waste and consumables must be autoclaved before removalfrom the site.
- Data management: Because the FDA expects faster access to research data from biologics facilities, data management systems must be asefficient and sophisticated as possible. An integrated laboratory service platform can enable best-in-class reporting, ensuring that facilities are operated to the correct standards—and on a cost-effective basis, as well.
Pharma IQ: What role do personnel play in supporting these more stringent regulations?
R Humphrey: Personnel make all the difference. It is no secret that regulated environments, particularly those guided by Good Manufacturing Processes (GMP) are difficult to manage, and most safety breaches occur because workers have not been properly certified or trained to work in biologics environments. Such highly controlled spaces require the right skills and ongoing training for compliance and consistent production.
Unfortunately, a facility staff that is highly trained in chemical labs will not automatically have the right skills and knowledge base for the different challenges of biologics. This may mean re-training and certifying support staff, or outsourcing to a provider with a good track record of managing biologics facilities with in-depth knowledge of the sector's needs.
Pharma IQ: Are today's facility management firms savvy enough for the job?
R Humphrey: The concept of outsourcing facility operations and management is new for many life sciences organizations, for whom managing operations in-house has long been the safest option. Now, however, a handful of providers have developed more specialized expertise—and the sophisticated technology platforms to support them—and are offering other relevant services, such as facilities ,safety management, equipment cleaning and maintenance, hazardous waste management, facilities-related compliance documentation and full-service laboratory management.
The right partner will have a strong mix of personnel and technology. Its personnel will be certified in complex regulated facility manufacturing practices, and will participate in ongoing training specific to human and animal health sites. Meanwhile, its technology platform will also support compliance by offering integrated and cloud-based systems that uphold standards across the entire portfolio.
Measuring value
The new pursuit of biological products, offers tremendous opportunity, but it also poses new challenges for Biopharma companies, for whom regulatory compliance is only becoming more complex. New scientific and professional expertise will be needed to develop the complex products and meet the additional challenges of biologics facilities protocols.
Transforming or building new life sciences facilities altogether is no small undertaking. But with BCC Research estimates the market for biologics will reach $252 billion in 2017, the investment is not just sensible—it is necessary for sustained success.
Interview conducted by Andrea Charles.
![]() |
Have Your Say Rate this feature and give us your feedback in the comments section below |