Medical devices: Rapidly adapting to meet demand in a crisis
Billy Sisk, Life Sciences Industry Leader EMEA at Rockwell Automation offers insight into how to start your digital transformation journey to meet market demands during Covid-19
Add bookmark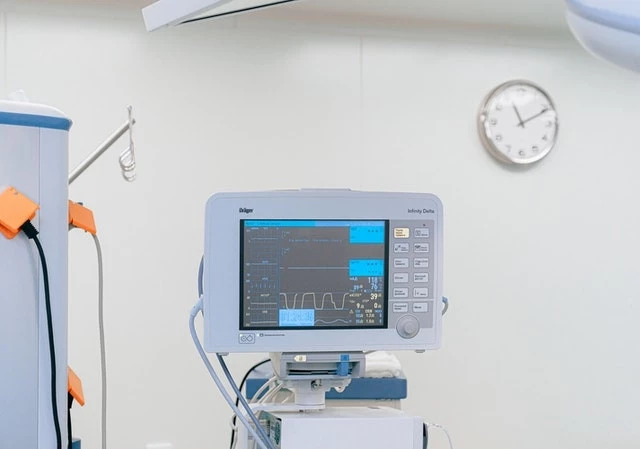
Global crises play havoc with demand patterns. The markets for certain products collapse overnight while demand for other goods skyrockets. At the time of writing, we are in the middle of the 2020 Covid-19 pandemic, and much of the upheaval we are experiencing is centered around medical devices.
Inevitably, equipment to treat and contain the virus – such as personal protective equipment (PPE), test kits, ventilators and respirators – are seeing unprecedented demand. This is in stark contrast to devices and equipment for non-essential surgeries, such as hip and knee replacements.
But this is just one example. If the pandemic is showing us anything, it is that demand patterns cannot be taken for granted. Medical device companies must have strategies in place to enable both business continuity and some degree of flexibility to meet changing demands, even after the current pandemic has run its course. I believe the digitally transformed manufacturer will be best positioned to succeed in this environment.
What are the key challenges for medical device manufacturers?
The medical device supply chain is currently under huge pressure, and any disruption to one link will send ripples through all the others. As demand increases, the opportunity for one of the links to fail also increases, threatening to impact delivery, manufacturing capacity and, ultimately, the patient.
This demand cannot always be met from elsewhere, either. Alongside the complexities presented by the technical, specialized nature of medical devices, the high level of regulation they are subject to is a challenge few from outside the industry can quickly master. That’s why the majority of high-profile ‘pivots’ from manufacturers in automotive and consumer goods that grabbed the headlines in the early weeks of the pandemic have come to little, and even life sciences manufacturers have had to overcome significant challenges to pivot production.
Additionally, the relaxing of certain standards to allow for the mass production of PPE has resulted in unfit-for-purpose products entering the supply chain. The NHS was forced to impound 400,000 protective gowns manufactured in Turkey after they failed to meet UK standards – Ireland experienced a similar problem with PPE from China.
-
The socially distanced factory
Medical device companies are taking a double hit in the current crisis: not only are they facing pressure to increase production volumes, but social distancing requirements to ensure staff safety are threatening to disrupt normal operations.
To adapt to the reality of the socially distanced factory, shifts must be staggered. If just one person on the line shows symptoms, the entire shift will need to self-isolate. The manufacturer may then need to rapidly onboard a new team that is unfamiliar with the manufacturing processes.
Crisis measures can also have a severe impact on areas such as maintenance and repair of critical manufacturing equipment. Much of this equipment originates overseas, with experts often flown in to attend to it. But today, such experts must quarantine for up to 14 days upon entering a country before being able to travel to a site, leading to expensive downtime, extra costs and inefficiencies.
-
Digital transformation as the solution
As we enter a period of sustained uncertainty, the companies that have set themselves up to quickly adapt their production and working practices are better positioned to weather these new challenges. What these companies often have in common is a high degree of digital maturity.
In some organizations, digital technologies such as augmented reality (AR) and advanced simulation tools are already providing solutions to many of the issues introduced by the socially distanced factory. By capturing manual activities in the virtual environment, they enable rapid knowledge transfer to train new shifts, reducing onboarding and training time, and bridging gaps in expertise within new or recently redeployed teams.
AR can also be used to guide operators or maintenance personnel, enabling remote experts to help local resources perform the critical tasks and maintenance required to recover from unplanned downtime situations. Meanwhile, simulation tools enable engineers to map equipment layouts and simulate the impacts on productivity and throughput that would arise as a result of layout changes. In this way, an optimal solution can be found without the need for experts to make physical adaptations on-site.
AR is a quick and easy-to-implement technology. But to meet the greater challenges presented by rapid changes in demand, manufacturing processes and supply chain visibility, a more holistic digital transformation is often required.
For example, businesses that have digitalized their end-to-end supply chain and are utilizing disruptive technologies such as AI and advanced analytics can already model for spikes in demand, pinpoint and account for disruption, and automatically feed this information into internal forecasts. These connected operations also enable them to realize cost savings and increased control without opening them up to the vulnerabilities engendered by a fully consolidated supply chain.
Once they have achieved a greater level of visibility and control, organizations can work on their own link within the chain, deploying flexible manufacturing technologies that allow them to scale their output and more easily pivot to create new lines or products without time-consuming and costly manual changeovers. The net result is an end-to-end supply chain that is better equipped to adapt to the spikes and troughs in demand that come in times of crisis.
-
Starting the transformation journey
Although the pandemic has put many activities on hold, manufacturers can still take the first steps toward digital transformation now. We have supported numerous companies on their digital transformation journeys, and have identified several critical success factors on the way.
Firstly, companies that understand their core objectives and outcomes are more successful. Having clear goals and KPIs at the outset enables the progress of any initiative to be measured. The organization must be aligned around these goals, and must understand the processes required to achieve them.
Secondly, there must be a full examination of the digital maturity level of current manufacturing operations. An organization needs to understand what is installed in its plants and assess the maturity of its infrastructure, processes, technology and people if it is to plan and achieve a digital transformation.
Following this assessment, an analysis of the technology available in the market needs to be conducted, and an understanding of the value it will bring to the company should be reached.
Finally, successful companies secure buy-in and senior-level sponsorship for their proposed digital projects. Such projects require cooperation across many business units; support from leadership is essential to driving out silo mentality and encouraging different parts of the business to work together.
-
Meeting demand in the new normal
There is no end in sight for the current crisis, at least in the immediate future. Instead, manufacturing and markets will slowly settle into what is being called ‘the new normal’, where ‘normality’ refers to a state of perpetual change and uncertainty. Medical device manufacturers must therefore put themselves in a strong position to respond to constantly shifting market conditions.
The key to successfully navigating these uncertain times is digital transformation. Those with a comprehensive view of the entire product lifecycle across their operations, manufacturing networks and supply chains will be better placed to deal with dramatic fluctuations in demand. This makes it all the more vital for those who have not done so to take the crucial first steps now.
For more industry updates on the Covid-19 pandemic, head to our keeping tabs on pharma content hub to dive in and to find out more about Rockwell Automation head to their website here.