Reinvigorating lab and office spaces to navigate the next normal
As the life sciences industry continues its essential research and development work in a physical lab, discover how organizations are taking the necessary steps to keep the workforce safe while attending to the needs of the business
Add bookmark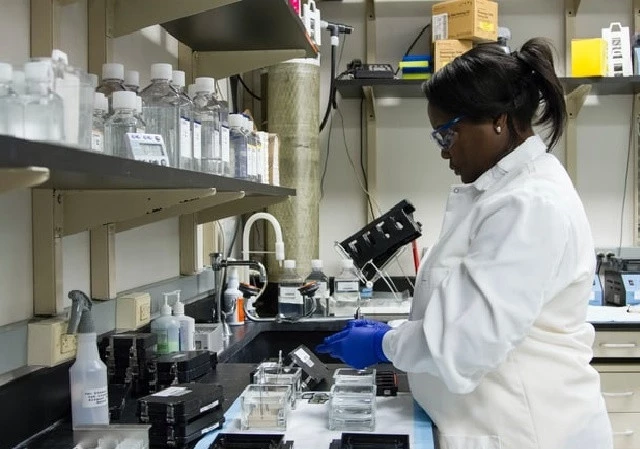
Pharmaceutical, biotechnology and medical device companies have been uniquely impacted by the Covid-19 pandemic, posing both opportunities and challenges for the life sciences industry. The pandemic has introduced opportunities in drug development with the creation of Covid-19 vaccines, therapies and diagnostics, but also created challenges in balancing corporate visions with production pipeline.
Hundreds of millions of patients across the globe depend on life sciences companies to help prevent and fight other critical health conditions such as cancer, diabetes and cardiovascular disease. GlobalData research shows highlights there are currently 310,575 clinical trials and overall 61,736 drugs in pipeline.
As life sciences organizations consider returning to laboratory and office spaces, there are some key questions that need to be answered:
- How should companies reinstitute scientists and reinvigorate lab spaces?
- What is the protocol for returning employees to office environments?
- What are the ongoing operational and safety considerations for employees?
- As the environment surrounding the pandemic evolves, what are some ways life sciences organizations can adapt to the next normal?
Steps to (re)activate your lab environments
It is essential for life sciences organizations to reactivate the necessary research and development (R&D) facilities to continue expanding production pipelines of new therapies. There are several immediate actions to take to serve the workforce and the priority needs of the business:
1. Analyze current footprint and workflow
Begin by taking a detailed look at your R&D footprint. Make a list of labs that have remained partially or fully operational and then separately identify the labs that are no longer operational or occupied due to the pandemic. Categorize these labs and then gather data on which scientists and other lab personnel have typically occupied the labs. The ultimate aim in gathering this data is to assess lab circulation patterns, map out critical workflows and build a foundation for facilities and equipment assessments.
2. Determine skills and prioritize delivery
Before you reactivate a lab space, it is important to set them up for success. Identify the skills of your scientists and technical talent currently working as well as additional employees you are considering for re-entry. Take these skills, match them with critical R&D deliverables and determine the facility infrastructure needed.
3. Conduct an activity-based assessment
Initiate the assessment by listing and reviewing the critical lab activities needed. Assess both operational and non-operational labs to determine which activities can be aligned and combined. Following that, prioritize your pipeline of projects so you can align with the skills of your employees and the necessary spatial distancing protocols.
4. Consider ways to minimize employee interaction, like minor reconfigurations
This is where data-gathering and initial assessments begin to pay off. Based on the number of lab personnel and the results of workflow analysis and density metrics, you can determine how to reconfigure where personnel are seated in the physical space. Many labs, depending on their flexibility, cannot fully reconfigure equipment, however, organizations can remove as many unessential items as possible.
Additionally, you can determine space capacity limits for labs and post these numbers at the entrance to each lab. Rotational scheduling combined with a reservation system are effective tools to elevate social distancing and minimize interaction. You can further determine next steps by answering the following questions:
- How does the lab receive support materials and compounds?
- Who accesses shared specialty equipment and how do they do so?
- Where can you leverage administrative controls to streamline flow and elevate social distancing?
5. Closely review and test your facility readiness
Depending on data collection and assessment results, each lab space will have significantly different utilities, heating, ventilation and air conditioning (HVAC) needs. Establish measures to review the status of lab support systems, conduct safe system starts and review the intricacies of HVAC systems. Conducting walk-throughs of each space will allow you to address equipment power availability, address timely issues and evaluate possible one-way directional personnel flows.
6. Install essential and creative solutions for employees
Life sciences companies can quickly and easily add “stop” signage to the front of doors or leading into areas that require caution. Adding hashing, arrows and footsteps as floor signage gives important direction to employees and reminds them of distancing measurements. As scientists focus on R&D, you can give them the security they need by installing plexiglass dividers between benches, hoods and other equipment. Creative ideas can achieve a positive impact and they do not have to break the bank. Some life sciences companies have installed touch free devices for entrances and exits to labs, for example. Consider simple and less expensive solutions like foot-operated door openers, using color schemes for masks and lab clothing to keep similarly focused lab teams aligned.
7. Create a thoughtful plan for ongoing lab operations
The little things go a long way. In your ongoing lab operations plan onminimizing the use of shared support items like stools, lab coats, computers and keyboards. Establish measures so employees know what has been used or what has not been used – for example, utilize green and red tape (for clean and not clean, respectively) on desks, chairs and other appropriate areas. With regard to supplies, plan for them to last for at least a week and coordinate delivery in designated areas outside of the lab. Additional areas to address for ongoing lab operations include waste management, evaluation of chemicals or other items with a short shelf life, supply stations and the ongoing management of personal protective equipment.
For five detailed checklists, floorplans and to discover more about operationalizing office space, download Return to work: A life sciences industry guide for navigating the next normal.